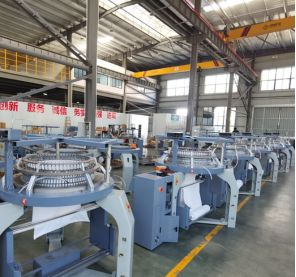
Causes of Monofilament Stripes and Preventive and Corrective Measures
Monofilament stripes refer to the phenomenon that one or several rows of coils on the surface of the fabric are too large or too small, or unevenly spaced compared to other rows of coils. In actual production, monofilament stripes caused by raw materials are the most common.
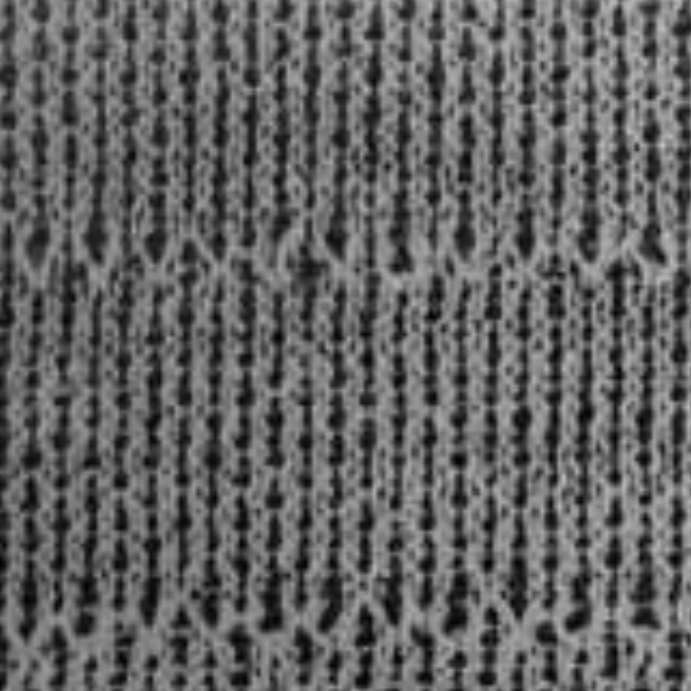
Causes
a. Poor yarn quality and color difference of monofilaments, such as tightly twisted yarn, chemical fiber filaments with different batch numbers, non-colored filaments or mixed yarns of different yarn counts, directly lead to the generation of monofilament horizontal stripes.
b. The size of the yarn tube is quite different or the yarn cake itself has convex shoulders and collapsed edges, resulting in uneven unwinding tension of the yarn, which is easy to produce monofilament horizontal stripes. This is because the different sizes of the yarn tubes will make their winding points and unwinding air ring diameters different, and the change law of the unwinding tension will inevitably be quite different. During the weaving process, when the tension difference reaches the maximum value, it is easy to cause different yarn feeding amounts, resulting in uneven coil sizes.
c. When using porous and ultra-fine denier raw materials for processing, the silk path should be as smooth as possible. If a yarn guide hook is slightly rough or the oil stains are solidified, it is very easy to cause multiple monofilaments of the raw material to break, and the color difference of the monofilament will also occur. Compared with the processing of conventional raw materials, it has more stringent requirements on equipment, and it is also easier to produce monofilament horizontal stripes in the finished cloth.
d. The machine is not adjusted properly, the needle pressing cam is too deep or too shallow at a certain place, which makes the yarn tension abnormal and the size of the coils formed is different.
Preventive and corrective measures
a. Ensure the quality of raw materials, use raw materials from famous brands as much as possible, and strictly require the dyeing and physical indexes of raw materials. The dyeing standard is above 4.0, and the coefficient of variation of physical indicators should be small.
b. It is best to use fixed-weight silk cakes for processing. Select silk cakes with the same winding diameter for fixed-weight silk cakes. If there are poor appearance formation, such as convex shoulders and collapsed edges, they must be removed for use. It is best to dye small samples during dyeing and finishing. If horizontal stripes appear, choose to change to non-sensitive colors or add horizontal stripe treatment agents to eliminate or reduce horizontal stripes.
c. When using porous and ultra-fine denier raw materials for processing, the appearance of raw materials must be strictly checked. In addition, it is best to clean the silk path and check whether each wire guide structure is smooth. During the production process, observe whether there are tangled hairs in the weft storage device. If found, stop the machine immediately to find the cause.
d. Ensure that the depth of the pressure gauge triangles of each feeding yarn is consistent. Use a yarn length measuring instrument to finely adjust the bending position of each triangle to keep the feeding amount consistent. In addition, check whether the bending yarn triangles are worn or not. The adjustment of the bending yarn triangles directly affects the size of the yarn feeding tension, and the yarn feeding tension directly affects the size of the formed coils.
Conclusion
1. Monofilament horizontal stripes caused by raw material quality are the most common in circular knitting fabric production. It is very necessary to select raw materials with good appearance and good quality for circular knitting machine production.
2. Daily maintenance of circular knitting machine is very important. The wear of some machine parts in long-term operation increases the horizontality and concentricity deviation of the circular knitting machine needle cylinder, which is very likely to cause horizontal stripes.
3. The adjustment of the needle pressing cam and the sinking arc during the production process is not in place, which causes abnormal coils, increases the difference in yarn feeding tension, and causes different yarn feeding amounts, resulting in horizontal stripes.
4. Due to the characteristics of the coil structure of circular knitting fabrics, the sensitivity of fabrics of different organizations to horizontal stripes is also different. Generally speaking, the probability of horizontal stripes in single-area fabrics such as sweat cloth is relatively high, and the requirements for machinery and raw materials are relatively high. In addition, the probability of horizontal stripes in fabrics processed with porous and ultra-fine denier raw materials is also relatively high.
Post time: Jun-07-2024